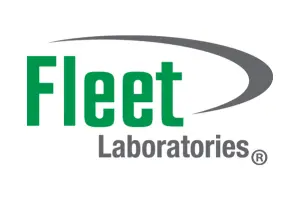
C.B. Fleet Laboratories Experiences Enhanced Communication with eMaint Dashboard Tools
Customer Since: 2014 | Industry: Manufacturing
C.B. Fleet Laboratories is a leading manufacturer of personal care and over-the-counter products, specializing in feminine hygiene, gastrointestinal products and infant care. Before the company found eMaint, they were searching for a CMMS system that was user-friendly and offered exceptional ongoing customer support. Using eMaint in accordance to their goals, C.B. Fleet has experienced improvements in uptime, increased company-wide communication and more.
BACKGROUND
C.B. Fleet began as a small pharmacy in Lynchburg, Virginia, with the mission to provide people with easy-to-use, innovative personal health and beauty care products. Today, C.B. Fleet Laboratories is a leading manufacturer of personal care and over-the-counter products, specializing in feminine hygiene, gastrointestinal products and infant care. In 2014, the C.B. Fleet leadership team met to discuss future plans. One important decision the team made was to identify a CMMS to support their mission, as their previous solution was inefficient and lacked a user-friendly interface. Marc Cote, Director of Engineering and Maintenance, was chosen to be a driver of the CMMS project.
THE CHALLENGE
C.B. Fleet researched ten different software providers, and decided to bring three providers on-site to test them. The company was in search of a CMMS system that was user-friendly and offered exceptional ongoing customer support. A service partnership was vital, as a challenge for the C.B. Fleet team was to develop a three-to-five year vision for the future. C.B. Fleet chose eMaint, and after a 30-day trial, they went live with an All In subscription.
IMPLEMENTATION
When C.B. Fleet chose eMaint as their CMMS solutions provider, they completed a validation for operational, process and data qualifications through the system. As part of their larger goal, the team wanted to achieve a proactive approach to maintenance via a high degree of excellence through revamped business processes. Five key pillars were identified as the focus for revamping processes: people, material management, workload management, basic care and reliability. The team kicked off implementation by interviewing mechanics to collect their insight into daily activities and identify which aspects of work were the most challenging to assess where C.B. Fleet stood as a facility. C.B. Fleet involved employees at all levels of the facilities management process and explained important metrics provided by eMaint.
With a better understanding of what improvements needed to be made, and with the eMaint Services team behind them, Cote and his team began working on the five key pillars. They started making changes in stockroom and materials management, workload management, Preventive Maintenance (PM) and compliance, labor charges and accountability of employees. C.B. Fleet now makes it a requirement for mechanics to provide a work order for every job. Documentation is also key for all work functions, including how to operate machinery.
RESULTS
Using eMaint in accordance with their goals, C.B. Fleet’s maintenance management team now has access to reports that allow them to track labor charges, as well as review completed work. With a system that is tracking assets, mechanics are able to search for parts and find what they need in less than five minutes. This has helped decrease downtime, and increase wrench time for employees. The company has also seen increased budget accountability by tracking material and labor expenses to work orders, and improved planning and scheduling by measuring weekly performance. Cote has reported that nearly every aspect of business is measured and reported to improve the already impressive changes in accountability, transparency and productivity within the company.
C.B. Fleet’s utilization of eMaint has caused a 50% reduction in reactive maintenance as well as a 35% decrease in reactive maintenance labor hours. The C.B. Fleet team has also utilized eMaints dashboard tool in a unique way. It is used as an internal communication tool, and a fountainhead for information. Cote updates the Dashboard on a weekly basis, posting how-to and informational videos of success, including recordings of eMaints Best Practices Webinars.
BENEFITS
“eMaint has been the key support system to energize our maintenance culture to shift to a proactive mode. Ensuring foundational data and overseeing the business in real-time has provided our organization with the ability to achieve our objectives. The power of information has been unleashed.”
Marc Cote, Director of Engineering and Maintenance, C.B. Fleet Laboratories