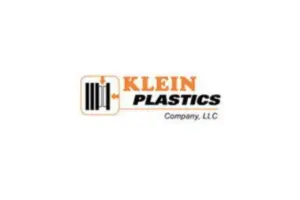
Klein Plastics Achieves a 20% Increase in
Overall Equipment Effectiveness (OEE) with eMaint CMMS
Overall Equipment Effectiveness (OEE) with eMaint CMMS
Customer Since: 2009 | Industry: Manufacturing
Klein Plastics produces plastic products and provides operational excellence for original equipment manufacturers and major suppliers of automotive parts, appliances, hand tools, and office furniture. In 2008, Klein Plastics was in great need of a more sophisticated CMMS solution, and eMaint was the perfect fit. After implementing eMaint, Klein Plastics saw various positive changes facilitated by eMaint, including 20% increase in overall Equipment Effectiveness, and an improvement in consistency, communication and productivity.
BACKGROUND
Klein Plastics, a subsidiary of Klein Tools, manufactures plastic products and provides operational excellence for original equipment manufacturers and major suppliers of automotive parts, appliances, hand tools, and office furniture. The Klein Plastics maintenance team, comprised of five technicians, implemented eMaint at its facility in Rockford, Michigan in 2008, after its successful eMaint implementation at a Klein Tools facility in Jonesville Michigan in 2001.
THE CHALLENGE
When Plant Manager Terry Geer came on board at Klein Tools in 2001, he advocated for a more advanced, web-based CMMS that had the ability to track machine uptime and failure codes. Geer explains: “We wanted to find a CMMS that could be accessed when I’m at home or on the road, and we didn’t want to have to maintain software on my own server.” eMaint’s web-based CMMS was the perfect fit for Klein Tools’ needs. In 2008, Geer moved on to manage the Klein Plastics plant in Rockford, which had been using an out-of-date in-house maintenance management system that was essentially nothing more than a system that generated time-based preventive maintenance reminders. Due to its success at the Klein Tools facility, eMaint was soon implemented at the Klein Plastics plant as well.
IMPLEMENTATION
Implementing eMaint’s CMMS at the Klein Plastics facility entailed bringing data over from their prior system. Once the data was imported, Klein Plastics focused on tracking parts, measuring uptime, and working toward building a knowledge base of historical data. Access to a Sandbox test account allowed Klein Plastics to experiment with many different aspects of eMaint. Complying with ISO and OSHA standards is a priority for Klein Plastics, as they are certified with both TS9000 and QS 9000 standards. eMaint also drives the 5 “S” Process (sort, shine, standardize, set and order, sustain). The system has helped improve consistency, communications and productivity across all shifts at Klein Plastics.
BENEFITS
- 20% increase in overall equipment effectiveness (OEE)
- Generates documentation and tasks for TS 9000 & QS 9000, Occupational Safety and Health Administration (OSHA) and lock-out, tag-out (LOTO) procedures compliance
- Provides the ability to forecast and track parts and associate them with assets
- Displays an overview of the overall machine status of the plant through a dashboard
- Improves communication between the Klein Plastics maintenance technicians on different shifts
- Troubleshoots repetitive repairs on over 600 assets
“I’m a solid believer in what eMaint has put out there. eMaint’s CMMS has helped us improve our OSHA and lock-out, tag-out safety procedures by enabling us to generate tasks and documentation.”
Terry G., Plant Engineer, Klein Plastics