What is a Computerized Maintenance Management System (CMMS)?
A CMMS, or Computerized Maintenance Management System, is a maintenance software for managing assets, work orders, inventory, preventive maintenance, condition monitoring, and more, designed to centralize data and boost asset uptime and utilization.
You can think of the best CMMS software as a command center for your maintenance and reliability programs: leaders can track work and gain insight into machine health and reliability, making it ideal for managing industrial facilities where machine assets are critical to production. CMMS software optimizes the use, availability, and lifespan of equipment, machinery, fleets, infrastructures, facilities, or operations.
Modern CMMS solutions are cloud-based and offer innovative features like AI, a mobile CMMS app, regulatory compliance tools, and multi-site or multilingual capabilities. They can also integrate with apps like ERP software, or tap into siloed production data from SCADA, PLC, and BMS systems. Leading CMMS platforms can even connect with condition monitoring sensors and software, giving teams the power of predictive maintenance.
Organizations can harness the power of CMMS software to save time, simplify their work, prevent downtime, reduce maintenance costs, and strengthen the reliability of their assets.
What is the Definition of CMMS? Key Term Meanings
A Computerized Maintenance Management System, or CMMS, simplifies maintenance management across assets, work orders, parts, reporting, and beyond, streamlining the organization and centralization of asset data – and strengthening uptime and reliability in the process. You may have heard the terms CMMS system, solution, platform, and software, and be wondering, what’s the difference? They’re all synonymous terms for digital systems for maintenance management. Enterprise Asset Managment (EAM) is another similar type of maintenance software, that also encompasses functionalities related to asset lifecycle management and global digital transformation. eMaint CMMS and EAM software does both.
What It Is: Key CMMS Features
Here’s a more detailed explanation of CMMS features and functionalities:
Work Order Management
Create, assign, and complete work orders and work requests. Automate work orders to trigger based on asset condition data from sensors or SCADA systems. Prioritize and escalate critical tasks automatically to keep downtime at bay.
Asset Management
Track assets, see their current status, and view detailed maintenance history. Organize assets into intuitive hierarchies and scan barcodes on the mobile app to instantly pull up related documents, tasks, or parts. Visualize asset condition in real-time with interactive floor plans and color-coded status pins.
Preventive Maintenance
Schedule recurring PMs for assets and include tasks, procedures, and parts. Advanced CMMS platforms also offer interactive drag-and-drop calendars for simplified PM planning. Level-load schedules and avoid resource conflicts with built-in PM scheduling alerts. Monitor PM compliance rates and generate on-time completion reports for auditors or leadership.
Parts and Inventory Management
Book spare parts for work orders and attach them to relevant assets. Monitor inventory levels and receive alerts when parts need to be reordered. Standardize and share inventory across sites to reduce costs and Mean Time to Repair (MTTR). Gain instant visibility into part usage trends and reorder thresholds through interactive dashboards.
Reporting, Analytics, & Dashboards
Design reports of maintenance activities and build dashboards to gain visibility into key processes and KPIs. Use pre-built templates or custom workflows to track KPIs like OEE, PM completion rate, or uptime. Drill down into the data to uncover hidden costs and optimization opportunities.
Mobile CMMS App
Manage maintenance from the palm of your hand, from work orders to booking parts. Premium CMMS apps allow offline work that syncs later. Scan QR codes to access asset histories and submit work requests in seconds. Upload photos or videos from the field to enhance communication and documentation.
Regulatory Compliance & Audit Dashboards
Easily build audit dashboards to demonstrate compliance. Review and report on records stored in a comprehensive audit trail. Safeguard key actions with electronic signatures. Track PM adherence, flag overdue tasks, and generate regulatory reports in a few clicks. Customize workflows to require approvals from quality, safety, or sanitation teams.
Integrations
Integrate your CMMS with your core business software, from SAP to Power BI, with API connections or through low-code integration. Tap into SCADA and PLC systems to access condition data. Eliminate data silos and automate time-wasting tasks by syncing maintenance data with ERP or procurement platforms. Use integration recipes to connect to key business systems with minimal IT overhead.
Predictive Maintenance
Connect to condition monitoring sensors and software to automate work orders based on condition data, evolving your strategy into predictive maintenance. Spot trends in vibration or temperature data before failure strikes, thanks to AI-driven diagnostics. Reduce Priority 1 failures by up to 90% and extend asset life through early intervention.
What are the Benefits of Using a CMMS Software?
There are many benefits of using CMMS software, both for operational efficiency and asset lifecycle. It allows teams to align their maintenance practices and activities with other departments and business goals. When you have a system that allows cross-departmental sharing of data, everyone’s job gets a little more efficient.
Some of top benefits of CMMS software include:
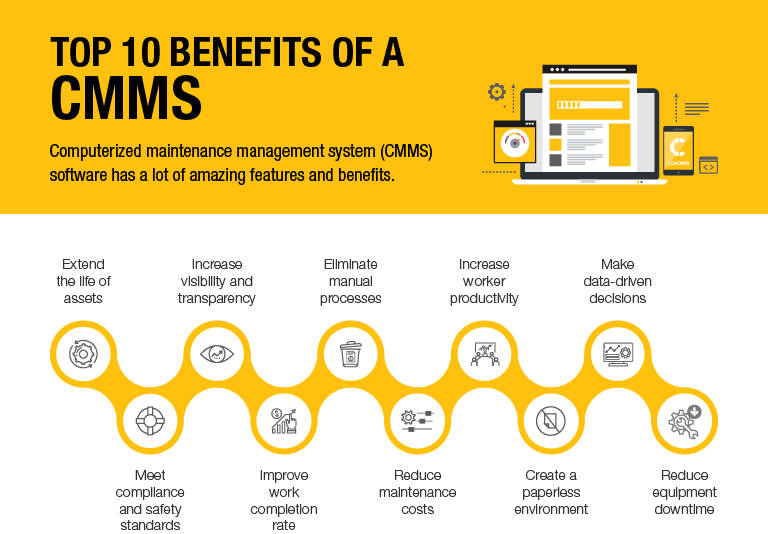
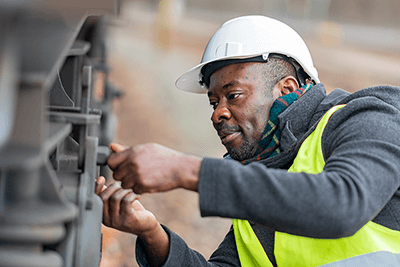
Healthy and Safe Environments
A CMMS can improve compliance with safety, health, and environmental regulations. When assets are properly maintained in a timely fashion, they’re less likely to have a failure that endangers workers or the environment. A CMMS can generate reports on incidents, defects, correction action histories, and help implement change management.
Workflow Visibility and Work Order Management
Work order software allows teams to visualize actions with dashboards and reports, helping every level of worker assess the current status and improve work order completion rates. Maintenance teams can quickly determine where an asset is, what work is needed, which parts are needed, who should complete the work, and when work should be performed. Once the work is completed, technicians can document their work directly in the CMMS.
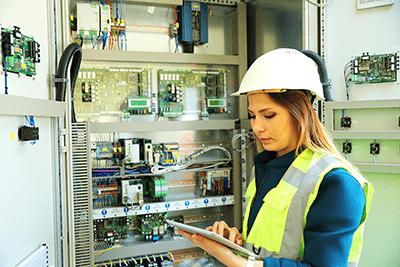
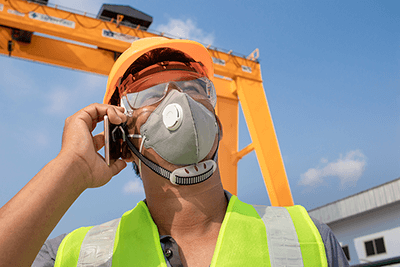
Mobile Workforce
Keeping field workers on the go can be challenging, especially if they have to spend time heading back to the office to update work orders or get their next assignment. The best CMMS software offers advanced mobility connectivity, so users rarely need to come back to the office. Remote team members can access everything they need right from the app and continue their fieldwork without interruptions.
Automation and processes
Automation saves time, reduces human error, and increases efficiency. Transitioning to a CMMS program allows users to automate many processes, like:
- Inventory reorders
- Scheduling shifts
- Assigning work orders by availability
- Preventive maintenance scheduling
- Compliance reporting

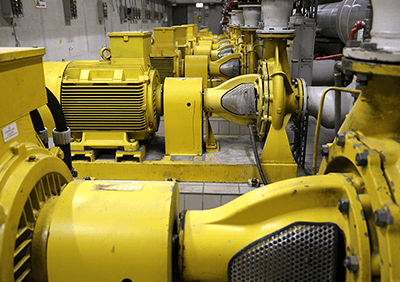
Asset Lifecycle Visibility
CMMS programs allow teams to track and manage asset health and lifecycle from pre-installation planning and engineering to decommissioning.
Prescriptive Maintenance
CMMS software helps teams move from reactive, preventive, and predictive maintenance to a prescriptive maintenance strategy. By integrating information like machine data from sensors and usage statistics, maintenance teams gain visibility into asset health. Then, the software can generate recommendations on what actions to take and when, which reduces costly downtime and improves asset lifespan.
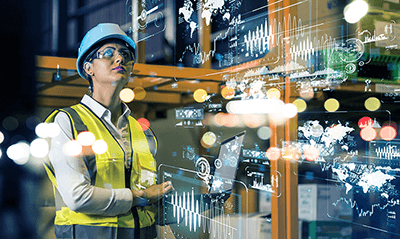
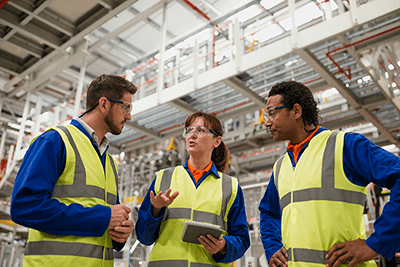
Regulatory Compliance and Audits
With compliance regulations from local, regional, state, national, and global organizations, it can be hard to keep up with audits. However, a CMMS can ensure regulatory compliance and create the digital paper trail that most compliance auditors look for to determine how well an organization meets all necessary standards.
Best CMMS Software
Best CMMS Software
Choosing the right CMMS can be a difficult process, especially when every provider seems to say they can do everything.
The best CMMS software includes features like managing work orders and parts inventory, automating predictive maintenance activities, enabling proactive maintenance strategies, and documenting maintenance activities for compliance. Solution providers should also provide robust training and support services before, during, and after deployment of software.
Why is eMaint the Best CMMS?
eMaint is the best CMMS and EAM software when it comes to implementation, support, and software Return on Investment (ROI) – read our reviews on G2 or Gartner to learn why.
Explore eMaint success stories to see the Fluke software in action, helping companies achieve everything from 95% uptime to $1.02 million in parts inventory savings.
4 Key Features to Look For in a CMMS
4 Key Features to Look For in a CMMS
Here are the key things to look for when choosing the best CMMS & EAM software for your needs:
1. Configurability and Ease-of-Use, from Mobile PMs to Desktop Dashboards
You dream it. We build it. Your CMMS team should be experienced in industry-specific configurations, from PM procedures to 21 CFR Part 11 workflows. A leading CMMS provider should train your team, and before you know it, your techs will be firing off work orders from mobile devices and designing KPI dashboards. Reporting configurability is especially key: how can you see if your team is successful, if you can’t quickly gain insight into work status and KPIs? Don’t forget integration systems like ERP and BI software – not every CMMS has seamless API integration like eMaint.
2. Dedicated, 100% In-House Support, Training, and Implementation
An estimated 80% of CMMS implementations fail to meet expectations due to a lack of training and support after the sale. It’s important to find a partner like eMaint that will provide the 100% dedicated, in-house support you need both before and after the sale with training, implementation support, and long-term professional services to keep your maintenance operations moving in the right direction.
3. Trusted Technology Partner for Life – from CMMS to Handheld Tools and AI
Go with a true technology partner like Fluke, invested in partnering with companies on the future of maintenance. eMaint, a Fluke software, is the only provider with the software, tools, and expert services you need for the age of predictive maintenance, backed by Fortune 500 company Fortive. The best CMMS will also empower you with AI-powered predictive maintenance, like eMaint.
4. Mobile CMMS/Work Order Software App
The best CMMS software has strong mobile CMMS capabilities. Maintenance operations should be driven by real-time, actionable insights, ready at your team’s fingertips no matter where they work from.
4. Experience in Global, Multi-Site Digital Transformation
Your CMMS/EAM provider should have decades of experience in managing global CMMS implementation and achieving multi-site standardization that delivers results in uptime, OEE, and production efficiency.
How Does CMMS Software Work?
CMMS software is essentially a database that contains all information about an organization’s maintenance and assets. It works by collecting and organizing data about work order creation and assignment, tracking, reporting, asset status, and more. Then, it puts that information into a single centralized database that different departments can access and use to streamline their processes. Among other things, a CMMS system functions as work order software to track maintenance orders and schedule tasks. It helps maintenance teams manage their workflows and minimize downtime.
Through integrations with vibration sensors and other condition monitoring tools, a CMMS and its database also let teams keep tabs around the clock on machine health and conditions, so they can implement condition-based maintenance.
Other key CMMS integrations, like ERP software, can help maintenance teams connect their operations to the purchasing and inventory functions used elsewhere in an organization. Those in operations or finance can benefit from visibility into inventory status or costs, supply contracting, and other maintenance functions.
While maintenance and reliability teams may spend their time focused on keeping machines running, today’s organizational environments make it necessary to have a CMMS that can communicate seamlessly with these other business systems.
What Does a CMMS Do?
The central function of a CMMS is to store, organize, and analyze maintenance data. That includes:
- Work order data
- Asset health data
- Scheduling and labor availability
- Inventory and spare parts
- Costs and budgeting data
- Regulatory and safety compliance data
CMMS software gives teams the organizational tools they need to increase efficiency, reduce downtime, standardize maintenance processes and workflows, and extend asset lifespan. CMMS solutions provide critical insights into equipment performance and maintenance needs, supporting proactive maintenance strategies and enhancing operational reliability.
Many of today’s leading CMMS solutions are cloud-based and offer innovative features like a mobile CMMS app, regulatory compliance tools, and multi-site or multilingual capabilities. They can also integrate with enterprise resource planning (ERP) and systems, applications, and products (SAP) software applications or tap into siloed production data from SCADA, PLC, and BMS systems. The best CMMS software, like eMaint, can even connect with condition monitoring sensors and software, giving teams the power of predictive maintenance.
What Are the Types of CMMS?
There are a range of CMMS solutions on the market, but they are generally divided into two types: on-premise or cloud-based CMMS. But which one is right for your operation? It depends.
On-premise CMMS solutions usually involve a higher upfront cost due to the expenses of purchasing and installing the necessary infrastructure to support the CMMS. They also require more in-house expertise. That’s because the installation process includes setting up a firewall and other IT infrastructure so that the software works smoothly on your server. Users of on-premise CMMS solutions also must pay for upgrades or additional solutions, including adding the necessary infrastructure to support the growth.
The trade-off? On-premise computerized maintenance management systems may offer a higher level of control and customizability, making it attractive to some larger institutions.
Cloud-based CMMS solutions are subscription-based and tend to cost significantly less since you don’t have to purchase hardware to keep on-site or hire in-house IT professionals to handle installation, maintenance, and upgrades. They are also easier to scale. Most cloud-based CMMS software providers issue free updates for existing users and include features to protect your data.
One of the chief benefits of a cloud-based CMMS is the ability to access data remotely. Workers in the field can access and update work orders through mobile apps, and decision-makers can log in and review asset health data remotely.
Why Use a CMMS?
Why Use a CMMS?
Computerized maintenance management software enables asset visibility across the entire organization. The flexibility and capabilities of a CMMS benefit everyone, from the teams tasked with day-to-day asset maintenance all the way to the leaders who make big-picture capital decisions. Traditional work order management systems keep work order and maintenance history siloed, limiting information sharing between departments and reducing the information available for decision-making and planning.
Thanks to the wealth of data captured by the CMMS, maintenance technicians can easily see which assets need maintenance. Asset prioritization ensures that teams will complete the most important repairs first, and automatic preventive maintenance scheduling makes sure specialists never forget routine maintenance tasks. Detailed checklists and procedures can ensure assets are maintained the same way no matter which technician is working on them.
Managers can see the status of an asset as well as its work history, such as which technicians worked on the asset and what tasks they completed. Audit trails and password-protected digital signatures provide audit-ready documentation without the need for tedious paper filing. Managers can also access reports to monitor maintenance hours and parts spending to get a clear picture of maintenance costs.
A CMMS provides a bird’s-eye view of assets across the organization, giving decision-makers visibility between multi-site facilities and allowing them to make data-driven decisions in real time. Instead of information being siloed to a single site, reports and metrics allow teams to compare assets and productivity across locations. Detailed asset histories give insights about whether assets should be repaired or replaced, and easy-to-use reports allow enterprise-level tracking of metrics like key performance indicators (KPIs) and audit dashboards.
Computerized maintenance management systems with integration capabilities provide even more information about the company as a whole. Software and hardware integrations incorporate information from sources like sensors and SCADA systems, and can even connect finance and ERP software.
Using a CMMS ensures team members have access to the information they need, no matter their role. This type of visibility is impossible with paper systems. Even electronic systems like spreadsheets, shared calendars, or other methods of maintenance tracking aren’t as effective or efficient as a computerized maintenance management system.
What is EAM?
What is EAM?
Enterprise asset management (EAM) is a strategy for managing company assets throughout their life cycles by planning operations and maintenance activities. The goal of EAM is to enhance asset performance, expand lifespan, and increase uptime. An EAM program generally synthesizes sensors, software, and tools to gather data. Equipped with this valuable knowledge, maintenance and reliability professionals can make maintenance profitable.
EAM programs take advantage of the following practices and more to ensure asset health:
- Asset lifecycle management
- Work order management
- Planning and scheduling
- Reporting and analytics
- Supply chain and inventory optimization
- Safety initiatives
- Financial management
A CMMS is a software command center for your EAM strategy, simplifying tactics like digital work orders, condition monitoring, and preventive maintenance scheduling.
What’s the Difference Between CMMS, FM, and EAM?
What’s the Difference Between CMMS, FM, and EAM?
CMMS software helps maintenance teams optimize their daily maintenance management duties including assigning and completing work requests, performing preventive maintenance tasks, and managing parts inventory and labor resources to maximize equipment availability.
Facility management software (FM) encompasses CMMS functions and also automates additional aspects of facility management, including budgeting, capital expense tracking, and contract management.
Enterprise asset management (EAM) focuses on the entire lifecycle of an asset from design and installation through ongoing maintenance through to disposal or replacement.
Choosing the Best CMMS Software Solution for Your Team
Choosing the Best CMMS Software Solution for Your Team
Choosing the right CMMS can be a difficult process, especially when every provider seems to say they can do everything.
The best CMMS software includes features like managing work orders and parts inventory, automating predictive maintenance activities, enabling proactive maintenance strategies, and documenting maintenance activities for compliance. Solution providers should also provide robust training and support services before, during, and after deployment of software.
4 Key Features to Look For in a CMMS
4 Key Features to Look For in a CMMS
While there are many critical features that can support your maintenance objectives, here are four must-haves for CMMS implementation:
- Configurability: There’s no one way to manage your maintenance operations. Every industry, company, and maintenance team has individualized needs. The best CMMS software is flexible enough to meet your unique requirements now and scale with you over time.
- Training and professional services: An estimated 80% of CMMS implementations fail to meet expectations due to a lack of training and support after the sale. It’s important to find a partner that will provide the support you need both before and after the sale with training, implementation support, and long-term professional services to keep your maintenance operations moving in the right direction.
- Ease of use: For any maintenance software, ease of use is key, especially for a software meant to make your job easier. Navigating and discovering insights should be simple and intuitive, and teams should be able to quickly get up to speed and begin using it effectively.
- Mobile CMMS/work order software app: The best CMMS software has strong mobile CMMS capabilities. Maintenance operations should be driven by real-time, actionable insights, ready at your team’s fingertips no matter where they work from.
Ultimately, the best CMMS for you is one that can be configured to fit your organization now and grow with you into the future.